自動車部品の面圧測定
(第3報,締付け方法の相違によるシール面圧の発生状況)
高 行男,長谷川達也,近藤俊也,島田智仁
1.緒言
以上のことより,第1報3)においては,自動車部晶の面圧測定の第1歩としてガソリンエンジンのシリンダヘッドガスケットの面圧発生状態を接触面圧,特にボア問の接触面圧に着目し,感圧フイルム法(富士プレスケール)と電着銅薄膜による接触面圧計測法4)5)を用いて調査した.その結果,感圧フイルム法では,「圧力を色で,数字で,一目でキャッチ」というキャッチフレーズ通り,容易に圧力を測定できた.また,電着銅薄膜による接触面圧計測法では,400MPa程度までの高い圧力(シリンダ外周近傍)を測定でき,感圧フイルム法に比べ,より微小な領域でより大きな圧力を測定できることが確認された.シリンダヘッドガスケット全体の面圧については,感圧フイルム法により,ボアの周囲とシリンダヘッドボルト穴の周囲の発色が集中など,面圧の発生状態を把握できた.特に重要なボア間の面圧については,高圧用プレスケールの測定可能範囲の上限値である130MPa以上の箇所の存在や,ボア間の中央付近では圧力がほとんど生じていないことが確認できた.
第2報6)においては,一般に同排気量においてガソリンエンジンよりも燃焼時に発生する筒内圧力が高いディーゼルエンジンのシリンダヘッドガスケットを対象とし,その面圧の実態を把握することを目的とした.接触面圧,特にシール性にとって重要なボア間の接触面圧に着目する場合,感圧フイルム法や第1報で用いた電着銅薄膜による接触面圧計測法では,面圧発生状態を正確に把握できない恐れがある.つまり,市販されている感圧フイルム法では,測定可能範囲の上限値である130MPaまでの圧力しか測定ができない.また,電着銅薄膜による接触面圧計測法の電着により作製した四角錐形状の微小な突起を利用する銅薄膜(銅薄膜ゲージI)では,400MPa程度の圧力までしか測定ができない.これは四角錐形状の微小な突起が400MPa程度でつぶれてしまうためである.そこで,新たに開発された電着面に生ずる表面粗さを利用する電着銅薄膜(銅薄膜ゲージU)によって面圧発生状態を調査し,900MPa程度までの圧力が測定可能であることを確認した.また,ガスケットの構造により発生する面圧が異なることを精度良く把握できるが,測定対象とする要素の材質や表面粗さによって圧力測定が困難なケースがあること,一度加圧すると元に戻ることはなく,締付け時の最大圧力が表示されていることに留意する必要があることが確認できた.
ところで,シリンダヘッドを組み付ける際,自動車整備書に従ってシリンダヘッドボルトの締付けを行うが,特に中型以上のディーゼルエンジンのシリンダヘッドボルトの締付け方法は,塑性域回転角度締付け法を推奨している.この作業は自動車整備士にとって大変労力を要するので,その必要性を認識することは,自動車整備士にとって重要な事柄である.そこで,本報告においては,シリンダヘッドボルトの締付け順序は自動車整備書どおりとするが,締付け回数を変更して,ボア間の面圧の発生状況を銅薄膜ゲージUにより測定するとともに,シリンダヘッドガスケットの厚さ測定を行い,シリンダヘッドガスケットのシール性を確保する上で,締付け回数の短縮ができないかを検討した.
2.実験方法
2.1測定エンジン
エンジンは,いすゞ・ビッグホーンに搭載されている4JXlディーゼルエンジンで,諸を表1に示す.シリンダヘッドガスケットの構造を図1に示す.4JX1エンジンで使用されているシリンダヘッドガスケットは,スチールラミネート(積層構成)であるが,シリンダボアのシール部の構造は,ステンレス板を3枚重ね合わせ,補強として内側に帯状のステンレスリングを入れ更に全体をステンレス板で包みこんだタイプである
表1 エンジン諸元値
Car name |
ISUZU・BIGHORN |
Form |
4JX1 |
Displacement |
2999 |
Cylinder arrangement |
4 Cylinders in line |
Combustion chamber |
Direct injection |
Valve mechanism |
DOHC |
Bore×Stroke mm |
95.4×104.9 |
Compression ratio |
19 |
Maxmum power kW |
160 (at3900min・1) |
Maxmum torque N・m |
30.4(at2000min−1) |
図1 4JX1ディーゼルエンジンのシリンダヘッドガスケットの断面模式図
電着面に生ずる表面粗さを利用した電着銅薄膜ゲージによるシリンダヘッドガスケットの面圧測定試験および厚さ測定素子を用いたシリンダヘッドガスケットの締付け時の厚さ試験を行った.測定条件は常温とし,シリンダヘッドボルトは新品を使用した.また,締付け順序は,表2の4通りとした.表中の3が自動車整備書の規定である
表2 締付け順序
Type |
lst |
2nd |
3rd |
1 |
49N・m |
− |
− |
2 |
49N・m |
600 |
− |
3 |
49N・m |
600 |
600 |
4 |
49N・m |
1200 |
− |
2.2.1電着銅薄膜による接触面圧計測法
一般に固体物質間の接触においては,巨視的には滑らかな表面であっても微視的には必ずある粗さを有しているため,その接触は微小な突起部分で行われる.巨視的には弾性接触と見なされる場合においても真実接触部である突起部分では,塑性変形が生じ真実接触面積は作用する圧力より変化する.この観点から,接触面積の変化に着目した接触面の圧力測定法が考案された4)5).その一つは,電着により作製した四角錐形状の微小な突起を利用する銅薄膜(銅薄膜ゲージI)であり,もう一つは,電着面に生ずる表面粗さを利用した電着銅薄膜(銅薄膜ゲージU)である.この2種類の銅薄膜ゲージを負荷圧力の大きさと測定面の粗さの違いによって使い分ける.本実験では銅薄膜ゲージUを使用した.
今回使用した銅薄膜ゲージUの作製は以下の通りである.まず,ステンレス円柱(直径42mm,長さ 200mm)の表面をパフ研磨により鏡面仕上げを行い,銅めっきを施して,電極より剥離したものである.銅薄膜ゲージUの厚さは約26μmで,その表面状況を図2に示す.
![]() |
![]() |
|
図2 銅薄膜ゲージUの表面状況 |
まず,圧力の測定について述べる.図3には銅薄膜ゲージUにおいて,電着銅薄膜の最終電着面に生ずる凸凹を利用して静圧測定をした結果である.静圧Psと接触面積割合rの関係を表示した図中の曲線は,最小二乗法を用いて二次近似を行ったものであり,式(1)で表される.この曲線では,Ps=0の時r=0でない.これは銅薄膜表面の結晶粒子が,負荷前の状態であっても平坦になっている部分があるためと考えられる.式中の係数a,b,Cを表3に示す.図3より,銅薄膜ゲージUは100〜900MPa程度の圧力が測定可能であるといえる.
r =aPs2+bPs+C ……(1)
![]() |
表3 係数 | |||||
|
||||||
図3 静圧Psと接触面積割合rの関係 |
![]() |
![]() |
図4 測定圧力に対する測定値のばらつきの関係 | 図5 測定圧力に対する誤差率の関係 |
次に圧力の測定精度について述べる.図4は作用静圧とその静圧に対する測定値のばらつきの関係を,図5は作用静圧と測定値に対する誤差率の関係を示している.図4より,測定値のばらつきは作用させた静圧の増加に伴い増大している.図5より,誤差率は作用させた静圧が低いと精度が悪くなる傾向がみられるが,静圧が低い場合を除けば誤差率は最大で±20%,平均で±10%程度となる.
図6にはボア間の測定箇所を,図7には銅薄膜ゲージの測定場所を示した.銅薄膜ゲージによる接触面圧計測方法は以下の通りである.
1. | 銅薄膜ゲージを挟む箇所は,シリンダボア間である.挟む順序は,シリンダブロック,銅薄膜ゲージ,シリンダヘッドガスケット,銅薄膜ゲージ,シリンダヘッドである. |
2. | 締付け手順は,表2に示した4通りの締付け順序である. |
3. | 締付け終了後5分間放置し,締付けと逆の順序でシリンダヘッドボルトを緩め,銅薄膜ゲージを取り出す. |
4. | 取り出したゲージ面を走査型共焦点レーザ顕微鏡(オリンパスOLSlOOO型)により観察し,粒子解析ソフトにより表面粗さの割合を算出して式(1)に示した校正式に基づいて圧力を求める |
![]() |
図6 ボア間の測定箇所 |
![]() |
図7 銅薄膜ゲージの測定場所 |
2.2.2 シリンダヘッドガスケットの厚さ試験の概要
厚さ測定素子を用いて締付けられた状態におけるシリンダヘッドガスケットの厚さをJISD3105に基づいて行った.厚さ測定素子は,市販されている150A用(直径2.0mm)のはんだを利用し,厚さは2.5mmに切断する.硬さはHVlOである.素子の形状は円柱となる.シリンダヘッドガスケットの測定箇所に測定素子の入る直径3mmの貫通穴を各燃焼室穴円周シール部に等間隔に8カ所あけた.
図8には厚さ測定素子の測定箇所を,図9には測定場所を示した.シリンダヘッドガスケットの厚さ試験の計測方法は以下の通りである.
1. | 測定箇所に加工したシリンダヘッドガスケットをシリンダブロック上面に乗せる. |
2. | 測定素子の入る直径3mmの貫通穴にワセリンを入れ,厚さ2.5mmに切断した厚さ測定素子を挿入する. |
3. | シリンダヘッドを乗せ,シリンダヘッドボルトを締付ける. |
4. | 締付け手順は,表2に示した4通りの締付け順序である. |
5. | 締付け終了後5分間放置し,締付けと逆の順序でシリンダヘッドボルトを緩め,測定素子を取り出し,その厚さをマイクロメータで測定する. |
![]() |
図8 厚さ測定素子の測定箇所 |
![]() |
図9 厚さ測定素子の測定場所 |
3.実験結果
3.1 シリンダヘッドガスケットの厚さ試験の概要
3.1.1 締付け順序1によるボア間の面圧
図10には,シリンダ1−2間と2−3間のボア間の圧力の調査結果を示す.
図10 締付け順序1によるボア間の面圧
各シリンダ中心を結ぶ線上において,1-2間と2−3間の中心を基準として,シリンダヘッドとガスケット間を上面,ガスケットとシリンダブロック間を下面として圧力分布を表している.上面においてボア間における圧力の生じ方は,ボア間中央の基準を中心に左右ほぼ対称で,ボア間中心から0.55mmと 3.27mm付近の2カ所の圧力が高いことがわかる.また,ボア間の中心と1.56mm付近では圧力がほとんど生じていないことがわかる.下面においては,ボア間中央の基準を中心にほぼ対称で,ボア間中心から1.05mmと 3.31mm付近の2カ所の圧力が高いことがわかる.また,ボア間の中央と1.81mm付近で圧力がほとんど生じていないことがわかる.上面も下面も面圧が高く発生している位置がある.この位置はシリンダの外周を2重にシールしていることを表わしている.シリンダボア側は幅広くシルし,ボア間中心側は局部的にシールしていることがわかる.
3.1.2 締付け順序2によるボア間の面圧
図11には,シリンダト2間と2−3間のボア間の圧力の調査結果を示す.
図11 締付け順序2によるボア間の面圧
締付け順序1と比較すると,ボア間中心側の面圧はほとんど変化していないが,シリンダ側の面圧が50MPa程度増加している.これは,シリンダヘッドガスケットに補強として内側に帯状のステンレスリングの上下方向に圧力が集中したためと考えられる.
3.1.3 締付け順序3によるボア間の面圧
締付け順序3は,自動車整備士が自動車整備書に従ってシリンダヘッドボルトを締付けた時の手順である.図12には,シリンダト2間と2−3間のボア間の圧力の調査結果を示す.
図12 締付け順序3によるボア間の面圧
各シリンダ中心を結ぶ線上において,1−2間と2−3間の中心を基準として,シリンダヘッドとガスケット間を上面,ガスケットとシリンダブロック間を下面として圧力分布を表している.上面においてボア間における圧力の生じ方は,ボア間中央の基準を中心に左右ほぼ対称で,ボア間中心から0.55mmと2.45〜3.27mm付近の2カ所の圧力は高くなり,シリンダ側よりもボア間中心側が高いことがわかる.また,ボア間の中心と1.56mm付近では圧力がほとんど生じていないことがわかる.下面においては,ボア間中央の基準を中心にほぼ対称で,ボア間中心から1.05mmと2.56〜3.31mm付近の2カ所の圧力が高くなり,シリンダ側よりもボア間中心側が高いことがわかる.また,ボア間の中央と1.81mm付近で圧力がほとんど生じていないことがわかる.上面と下面において,シリンダ側よりボア間中心側が高いのは,シリンダボアのシール部の構造が鋼板を3枚重ね合わせ,補強として内側にリングを入れ更に全体をステンレス板で包んでいることによると考えられる.全体を包んでいる.ステンレス板はプレスでピード(凸凹)を形成したことにより,ピードの凸方向はシリンダヘッドとシリンダブロックの接触方向となり,その凸部に圧力が集中したためと考えられる.締付け順序2と比較すると,シリンダ側の面圧は上,下面ともほとんど変化していないが,ボア間中心側の面圧は100MPa程度増加し,250MPa程度になっていることがわかる.
250MPa程度の圧力が発生していることは,FEM解析によっても認められる7).
3.1.4 締付け順序4によるボア間の面圧
図13には,シリンダト1-2間と2−3間のボア間の圧力の調査結果を示す.
図13 締付け順序によるボア間の面圧
締付け順序3すなわち,自動車整備書に従ってシリンダヘッドボルトを締付けた時の結果と比較すると,面圧の発生状況は上,下面ともほぼ同じなので,締付け回数を2回にしてもガスケットのシール性は保たれていると考えられる.
3.2 シリンダヘッドガスケットの厚さ試験の結果
3.2.1 締付け順序1によるシリンダヘッドガスケットの厚さ
図14には,締付け順序1によって締付けた時の燃焼室穴シール部8カ所におけるシリンダヘッドガスケットの厚さの調査結果を示す.
図14 締付け順序1による測定素子の厚さ
図より,第1シリンダの3番と第2シリンダの3番,7番,第3シリンダの3番,7番,第4シリンダの7番は,それ以外の箇所より厚いことがわかる.これらの箇所はすべてボア間である.これらの箇所がその他の箇所より厚くなっているのは,シリンダ間のガスケットの構造において,鋼板がボア間のみ3枚重ね合わせとして補強してあるため,測定素子の厚さが変化しにくかったと考えられる.また,第2と第3シリンダの中心を基準とすると,測定素子の厚さ状況は,左右,上下ともほぼ対称となっていることもわかる.
3.2.2 締付け順序2によるシリンダヘッドガスケットの厚さ
図15には,締付け順序2によって締付けた時の燃焼室穴シール部8カ所におけるシリンダヘッドガスケットの厚さの調査結果を示す.
図の各測定値を線で結んだ8角形の面積を締付け順序1の時の面積と比較すると,順序2は小さいことがわかる.これは測定素子に締付け圧力が増加したことによる.
図15 締め付け順序2による測定素子の厚さ
3.2.3 締付け順序3によるシリンダヘッドガスケットの厚さ
締付け順序3は,自動車整備書に従ってシリンダヘッドボルトを締付けた時の手順である.図16には,締付け順序3によって締付けた時の燃焼室穴シール部8カ所におけるシリンダヘッドガスケットの厚さの調査結果を示す.
図16 締付け順序3による測定素子の厚さ
図より,第1シリンダの3番と第2シリンダの3番,7番,第3シリンダの3番,7番,第4シリンダの7番がその他の場所よりも厚いことがわかる.これらの箇所はすべて燃焼室穴シール部間で,その他の箇所より厚くなっているのは,既に述べたように,シリンダ間のガスケットの構造において,鋼板が燃焼室穴シール部間のみ3枚重ね合わせとして補強してあるため,測定素子の厚さが変化しにくかったと考えられる.また,第2と第3シリンダの中心を基準とすると,測定素子の厚さ状況は,左右,上下ともほぼ対称となっていることもわかる.
図の8角形の面積を締付け順序2の時の面積と比較すると,順序3は小さいことがわかる.これは測定素子に締付け圧力が増加したことによる.
3.2.4 締付け順序4によるシリンダヘッドガスケットの厚さ
図17には,締付け順序4によって締付けた時の燃焼室穴シール部8カ所におけるシリンダヘッドガスケットの厚さの調査結果を示す.締付け順序4は,順序3と比較すると,8角形の面積はほぼ同じで,測定素子の厚さもほぼ同じであることがわかる.このことから,シリンダヘッドガスケットの厚さはほぼ同じと考えられる.
図17 締付け順序4による測定素子の厚さ
図18はすべての締付け順序における第2燃焼室穴シール部の測定素子の厚さを示す.この図より締付け順序2は,順序1より測定箇所8カ所すべてが0.02mm程度薄くなっていることがわかる.また,図より締付け順序3は,順序2より測定箇所8カ所すべてが0.03mm程度薄くなっていることがわかる.図において締付け順序4は,順序3と比較すると測定素子の厚さはほぼ同じである.したがって,締付け順序4での測定素子の厚さは順序3の時とほぼ同じといえる.よって,自動車整備書に従ってシリンダヘッドボルトを49N・m+600°+600°の3回に分けた締付け手順を,49N・m+1200°の2回に短縮しても,燃焼室穴シール部周りのシール性は見かけ上保たれていると考えられる.ただし,燃焼室穴シール部周り以外の箇所については今後の検討課題である.
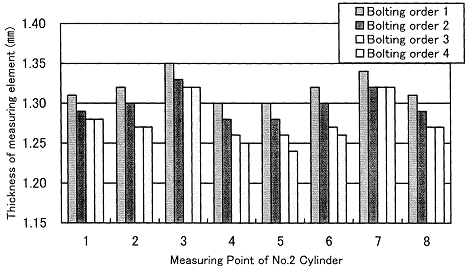
図18 第2燃焼室穴シール部の測定素子の厚さ
4.結論
ボア間の面圧の発生状況とシリンダヘッドガスケットの厚さの測定を行い,シリンダヘッドガスケットのシール性を確認するとともに,締付け回数の短縮ができないかを検討した.主な結果は以下の通りである.
(1)表面粗さを利用した電着銅薄膜(銅薄膜ゲージU)による接触面圧計測法では,締付け回数を増やすことによりシリンダボア間の面圧が増加する.自動車整備書に従ってシリンダヘッドボルトの締付け,すなわち,49N・m+600°+600°の3回に分けて締付けた時と49N・m+1200°の2回に分けて締付けた場合のボア問の面圧発生値が250MPa程度以上となり,両者の面圧発生状況の結果には著しい差異は認められない.
(2)厚さ測定素子を用いたシリンダヘッドガスケットの厚さ試験では,締付け回数を増やすことによりシリンダヘッドガスケットの燃焼室穴シール部周りの厚さが減少する.シリンダヘッドガスケットの厚さ試験の結果においても,自動車整備書に従ってシリンダヘッドボルトの締付け,すなわち,49N・m+600°+600°の3回に分けて締付けた時の測定素子の厚さと49N・m+1200°の2回に分けて締付けた場合の結果には著しい差異は認められない.
上述のように,ボア部周辺のシール性は,見かけ上は問題ない結果となった.今後,ボア部周辺以外のシール性やボルトの軸力の安定性などを検討する必要がある.
終わりに,本研究の遂行にあたり,助言をいただいた鳥取大学 北岡征一郎教授,協力いただいた同大学院 吉田雅人君に謝意を表する.また,多大なご助力をいただいた(株)石川ガスケット専務取締役 宇田川恒和氏に深謝する.
付記 著者の近藤俊也,島田智仁は,本学専攻科自動車工学専攻の第9期(2001年度)生である.
参考文献
1)自動車用機関のシリンダヘッドガスケット,日本工業規格D3105(1992).2)高行男,長谷川達也,北岡征一郎,島岡俊行,銅薄膜ゲージによるシリンダヘッドガスケットの面圧測定,自動車技術会2001年春季学術講演論文集,No.70−01(2001),P.17.
3)高行男,長谷川達也,井藤賀久岳,杉原中也,岡本安広,自動車部品の面圧測定(第1報,ガソリンエンジンのシリンダヘッドガスケット),中日本自動車短期大学論叢,第31号(2001),P.1.
4)北岡征一郎,坪田淳一郎,永橋 豊,岸 武保,電着銅薄膜による接触面圧計測法,日本機械学会論文集,64巻619号A編(1998),P.145.
5)北岡征一郎,長谷川達也,島岡俊行,電着銅薄膜による接触面圧計測法,日本機械学会中国四国支部講演論文集,No.015−1(2001),P.3.
6)高 行男,長谷川達也,自動車部晶の面圧測定(第2報,ディーゼルエンジンのシリンダヘッドガスケット),中日本自動車短期大学論叢,第32号(2002),P.1.7)高行男,長谷川達也,北岡征一郎,宇田川恒和,エンジンのシリンダヘッドガスケットに対する新たな面圧測定法,自動車技術会2002年春季学術講演論文集,No.70−02(2002),P.17.