アライメント・シミュレータ
徳島工業短期大学 花野裕二、島田 清、佐藤 員暢
keywords:ホイールアライメント キヤンバコントロール、トーコントロール、コンプライアンスステア
1.まえがき
自動車性能は高速道路網の整備充実に伴い向上してきた。タイヤはサスペンションによってボディーにつながれているが、その対地姿勢はサスペンションパーツがどのような配置で取り付けられ、それらがどのような働きをするかによって決まる。タイヤが路面に対してどのような位置関係になっているかを示すのがホイールアライメントであり、アライメントによって自動車の操縦安定性が大きく影響を受ける。その為、現在のサスペンションにおいては、操舵時、加速時、制動時その他走行中の車両姿勢の変化に合わせてアライメントを制御する機能を持たせたものが多くなっている。
現在のサスペンション整備では、停止状態でのホイールアライメント点検整備が一般的であり、実走行中のアライメントが実際どのようになっているかは把握できていない。そのため経年変化によってブッシュ類が硬化するなどにより、所定のアライメント制御が行えず自動車本来の機能が発揮できない場合がある。このようにサスペンション機能、構造の進歩に整備が伴っていないのが現状であり、サスペンションの性能認識と整備に新たな教育の必要性が求められている。
そこで、車両のタイヤに走行中加わる負荷(横方向、前後方向)によるアライメント(キャンバ角、トー角等)変化を台上で測定できる装置を試作し、車両走行時のアライメント変化が解析でき、実習教材として活用できる目途を得たので、それにつき報告する。
2.アライメント・シミュレータの概要
測定分析は、実車における一輪のタイヤ接地面に走行中加わる前後、左右の力を与えることができるように、水平移動できる平板を油圧シリンダで動かす形式とした。供試車両は他の三輪で試験場の路面に自重で固定されているが必要に応じ床面に設置したアンカにより固定ベルトで固定することも可能な構造とした。また、試験中は車両が移動しないように駐車ブレーキ及びフートブレーキをかけた状態として測定することとした。車両を固定した状態で、任意の一輪に加える前後左右の荷重を操作盤上で設定し、値をデジタル表示(最小目盛1N)できるようにした。(写真1、2、3)
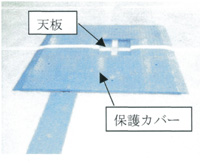
写真1.アライメント・シミュレータ概観
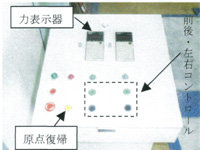
写真2.アライメント・シミュレータ制御盤
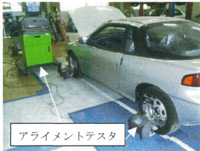
写真3.車両セット状態
本装置の図面を図1に、仕様を表1に示す。
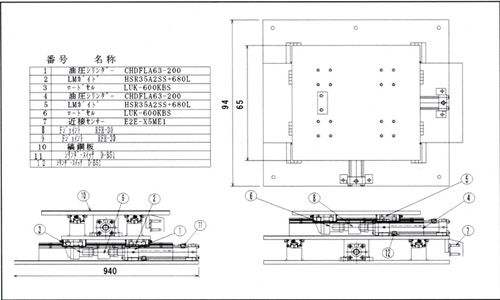
図−1試作アライメント・シミュレータ
3.アライメント・シミュレータの動作確認
天板の変位測定は、試験車両のホイール端と地面に設けた基準位置との間の移動距離をデジタル・ノギスを利用して測定を行った。まず、負荷荷重が小さい場合のアライメント変化を測定した。
表1 アライメント・シミュレータスペック
天板寸法 | 650mm×650mm | |
ストローク | 左右 | ±100mm |
前後 | ±100mm | |
最大負荷 能力 |
左右 | ±2.5kN |
前後 | ±2.5kN | |
耐荷重 | 38kN |
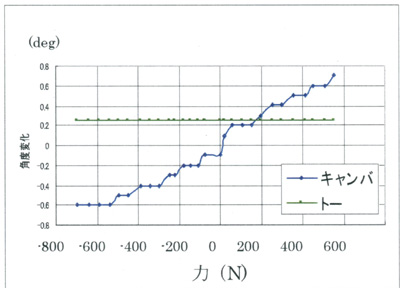
図・2 加負荷横方向(後車輪)
後輪に負荷を加えた場合のキャンバ、トーの変化を図2に示した。タイヤに内向きの荷重が加わると+キヤンバになる様子がわかる。また、トーの変化はない。
図−3 加負荷横方向(前車輪)
同様に前輪に負荷を加えた場合のキャンバ、トーの変化を図3に示した。キャンバ変化は後輪と同樺であるが、前輪の場合は車両内向きの力によりトー・アウトになることが観測された。以上の変化は供試車両のサスペンション形式から見て妥当なものであると判断できる。
以上のことから、本装置により基本的な測定解析が行えることがわかった。しかしながら、負荷を実車相当の値まで増大させていくと、タイヤと天板との間にスリップが生じることが判明した。その為、より実車に近い状態での測定ができるよう装置の改良を行なうとともに、測定に適した車両の条件を見出す実験を行なった。
4.実験方法及び考察
今回実験に使用した車両仕様を表2に示す。車両点検としてブレーキ廻りの点検及び、調整後、前回同様に床面と車両間を固定ベルトにより固定し、駐車ブレーキ及びフートブレーキをかけた状態で行った。
表−2 供試車両スペック
車両質量 | 10200 N | 独立懸架式サスペンション | |
F輪荷重(測定輪) | 3100 N | フロント | トランスバース・リンク式 |
R輪荷重 | 2000 N | リ1ヤ | パラレル・リンク式 |
まず、左右方向に負荷をかけた状態についてのスリップ限界点について測定を行った。天板に縞鋼板を使用した場合及び、天板に摩擦材としてサンドペーパを貼り付けた場合の前輪のスリップ限界点の比較を図4、図5に示した。,図から明らかなように縞鋼板でのスリップ限界点が負荷約±750N程度であったのに対し、天板にペーパを貼り付けた場合では約±1870N程度と約2.5倍程度のグリップカが発生していることがわかった。これをタイヤ接地荷重から摩擦係数を求めると約0.6となり、ほぼ実路面(ドライアスファルトで0.7〜0.85)とタイヤの摩擦係数に等しい値となった。
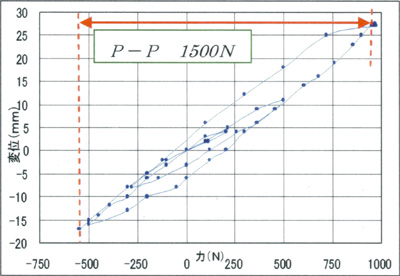
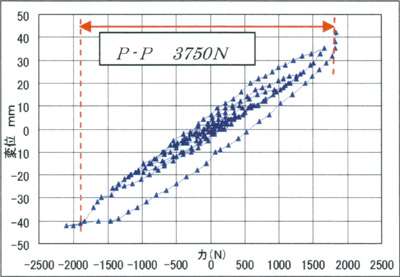
次に、前後方向に負荷をかけ同様にスリップ限界点について測定を行った。図に示すように、天板が縞鋼板の場合では、スリップ限界点が約±600Nと低い値であるが、天板にペーパを貼り付けた場合では約2倍程度グリップカが発生していることが図7から分かった。
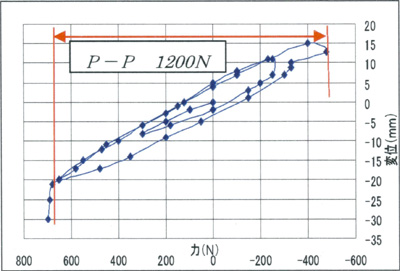
図−6 縞鋼板(前後方向負荷)
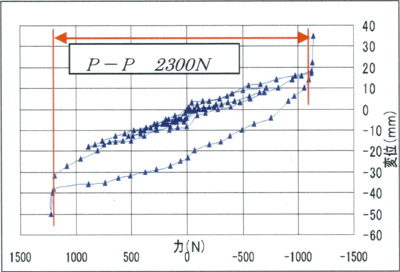
図−7 ペーパ張付け天板(前後方向負荷)
しかし、左右方向に負荷をかけた場合と比較してみると、左右方向ではスリップ限界点が約±1800Nで発生しているのに対し、前後方向に負荷をかけた場合では約±1100N前後と測定値の増加率が低く、左右、前後方向負荷時とで開きが生じた。
実験方法としては前後、左右方向ともフートブレーキをかけた状態で測定している為、本来スリップ限界点は左右、前後方向負荷をかけてもほぼ同じ値となるはずである。
そこで、その原因を探るべく、タイヤと天板接地部分に前後負荷力が加わったとき何が起きているのかを確認する為、負荷をかけたときの接地部分の動きを再度確認してみることにした。確認方法としては、車両フェンダー部に基準マーク及び、タイヤには中心線を貼り付け、負荷をかけたときのタイヤの動きを写真撮影し分析してみることにした(写真・4)。
![]() |
![]() |
![]() |
![]() |
写真-4 前方向負荷によるタイヤの動き
写真-4からわかるように、負荷力が800Nあたりよりタイヤに回転方向の動きがみられた。タイヤと天板間にすべりは生じておらず、タイヤ自体はグリップしているが、タイヤが負荷増大状態で回転している。すなわち、ブレーキが滑っていることが確認できた。そこで、ブレーキに倍力作用をかけるためエンジンを始動しブレーキを強く踏んだ状態で再度実験を試みた。測定結果を図-8に、タイヤの動きを写真−5に示す
凰且から明らかなように、無倍力時に比べ約2倍の約±1750N程度まで測定可能なことが確認できた。
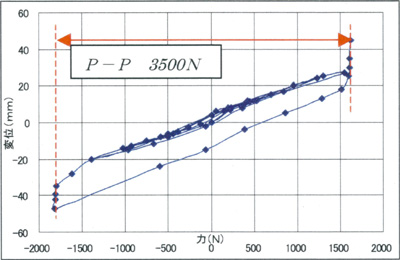
図−8 ペーパ貼付天板(倍力時による前後方向負荷)
![]() |
![]() |
![]() |
![]() |
写真・5 前方向負荷(倍力時)によるタイヤの動き
5.結論
・本装置(天板へのサンドペーパ貼付)によって、タイヤと天板間の摩擦係数を上げ実車に近い負荷 を加え走行中のアライメント変化を台上で測定、解析することが可能となった。
・前後方向負荷については、ブレーキが容易に滑り出すことがわかった。従って、エンジンをかけ倍力装置を働かせた状態で、しっかりとブレーキを踏んでいれば左右方向負荷と同様の測定が可能である。
・精度を向上させる為には、車両の接地、固定方法など、まだ工夫の余地が残っていると思われるがそれらについては、今後の課題としたい。
6.あとがき
・本アライメントシミュレータは、当面の狙いをほぼ達成できたので、本装置とアライメントテスタ を使用し、タイヤに負荷を与えた状態でのアライメント変化(キャンバ、ト一角)について自動車 整備士教育実習にも活用できるよう実習内容、方法について検討してゆきたい。,
参考文献
1)宇野高明
:車両運動性能とシヤシメカニズム
2)安部正人 :自動車の運動と制御
3)熊野 学 :サスペンションの仕組みと走行性能
4)坂井秀夫 :タイヤ工学